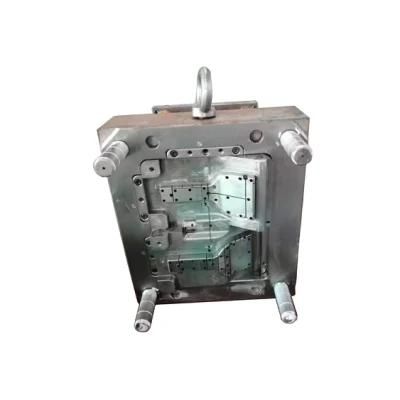
Injection Plastic PE PP PS ABS Mold for Consumer Product
Dongguan Howe Precision Mold Co., Ltd.- Application:Car, Furniture, Electronic, Hardware, Household Appliances, Commodity, Home Use
- Process Combination Type:Single-Process Mode
- Plastic Material:PE
- Mould Cavity:Multi Cavity
- Shaping Mode:Injection Mould
- Surface Finish Process:Polishing
Base Info
- Mold of Steel Suppliers:Finkl,Assab,Daido,Lkm,Buderus
- Mould Material:M2, Skh-9, Skh-51, M35, M42, Asp23
- Gate Type:Side Gate,Sub Gate,Pin Point Gate,Edge Gate etc
- Mold Life:>300, 000 Times
- Mold Standard Components:Hasco, Misumi, Meusburger, Dme, etc
- Product Name:Plastic Injection Molds
- Customized:Customized
- Standard:DME
- Certification:ISO
- Installation:Fixed
- Design Software:Pro-E
- Runner:Cold Runner
- Model NO.:HW-1034
- Payment We Support:T,T, Paypal
- Transport Package:Wooden Cases,Air,Sea
- Specification:Custom
- Trademark:HOWE or Custom
- Origin:China
- HS Code:8522901000
- Production Capacity:40sets,Month
Description
Mould Trade Process
1. 3d Design/Samples for quotation: According to 3D drawing or samples for quotation.
2. Negotiations: Including the price of moulds, moulds sizes, material for cores & cavities, the weight of the product, part cost, payment, moulds lifetime, delivery, etc.
3. Purchasing Order: After the customer confirming the mould design and quotation.
4. Making mold: Confirm drawing, start to do DFM,mold flows and mold detail agreed with the customer, start production.
5. Production schedule: Every week we will feedback to the customer mold progress(picture).
6. sample shoot: We provide the moulds test samples for confirmation(about 10-15 pieces), then, get your signature sample, mass production.
7. Package: Wooden case for moulds, cartons for parts, or as your requirements.
8. Delivery: deliver goods by air or by sea.
Quality Control
Work Shop
Sample Room
Packaging & Shipping
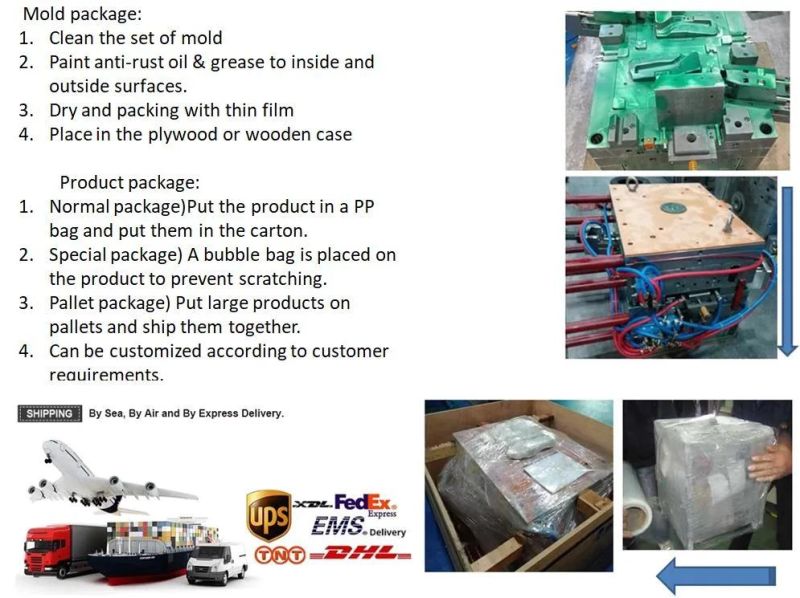
FAQ about Plastic Injection Mold
Q1: What kind of molds do you make? Plastic injection mold, Compression mold or something else?
A1: We are mainly making plastic injection mold and die-casting mold.
Sometimes we also make rubber molds according to our customer's requirements.
Q2: Do you build hot runner plastic moulds?
A2: Yes. We build hot runner Plastic Moulds and specialized in many different systems, such as DME, Master, Mastip, Hasco, Yudo, Incoe, Husky, etc.
The manifold recommended for your tool is selected to meet your individual needs.
Q3: What types of files do you accept (drawings)?
A3: With our CAD systems we can accept the following files:STP, IGS, DXF, DWG, Cad Key PPT, STL, X_T, CATIA, UG files, etc.
Q4: What kind of steel do you use for plastic mouldings?
A4: We can use any type of steel appointed by customer or popular in the market.
Such as P20, 718, 8407, NAK80, H13, S136, DIN 1.2738, DIN 1.2344, etc.
Q5: Can you provide the steel certificate and heat-treatment certificate?
A5: Yes, We can provide steel certificate or hardness certificate to prove.
Q6: Can you make the texture/text/heat-treatment/nitriding for the injection mold plastic?
A6: Yes, As a plastic mold factory, we have long-term cooperated subsidiary factories that do those processes.
They are professional and well reputed in our local market.
Q7: How long is the lead-time for a plastic injection mold?
A7: It all depends on the mold's size and complexity. Normally, the lead time is 25-45days.
If the Plastic Mouldings are very simple and not big size, we can work out within 15 days.
Q8: Do you make spare parts for your customer?
A8: Yes, we will provide spare parts for the mold if needed or required by clients.
Q9: How do you pack the plastic moulds?
A9: We pack the plastic moulds with a wooden box.
There are the main 3 operation steps.
First Step: We daub some rust preventive oil on the mold.
Second step: We pack the mold with thin plastic film to avoid moisture.
Third step: We put this plastic film packed mold in a wooden box, and fix it to avoid any movement.