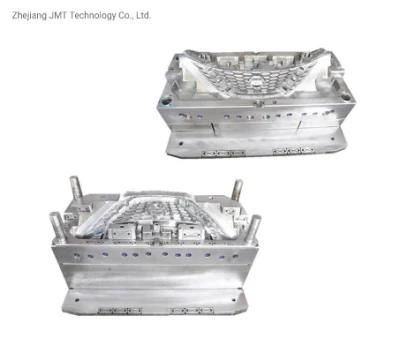
Auto Exterior Mould / Grill Plastic Injection Mould
Zhejiang JMT Technology Co., Ltd.- Plastic Material:PA66
- Mould Cavity:Single Cavity
- Surface Finish Process:Polishing
- Shaping Mode:Injection Mould
- Warranty:1year
- Process Combination Type:Single-Process Mode
Base Info
- Trademark:JMT Technology
- Specification:1650*520*500
- Transport Package:Wooden Case
- After-sales Service:1year
- Customized:Customized
- Standard:HASCO
- Certification:TS16949, ISO
- Installation:Fixed
- Design Software:UG
- Runner:Hot Runner
- Application:Car
- Model NO.:JMT2021395
- Origin:China, Zhejiang, Taizhou
- HS Code:8480710000
- Production Capacity:650 Set,Year
Description
Basic Info.
Model NO. JMT2021395 Application Car Runner Hot Runner Design Software UG Installation Fixed Certification TS16949, ISO Standard HASCO Customized Customized After-sales Service 1year Transport Package Wooden Case Specification 1650*520*500 Trademark JMT Technology Origin China, Zhejiang, Taizhou HS Code 8480710000 Production Capacity 650 Set/YearProduct Description
Mold details:Type: | Injection mold | Core surface finish: | Polish |
Production Material: | PA66 + 10GF | Cavity surface finish: | Texture |
No of Cavities: | 1 | Injection System | Hot Runner |
Core Material: | 8407 with heat treated | Type of gating: | Direct gate |
Cavity Material: | 8407 with heat treated | Ejection system: | Ejection pin |
Slider material: | SKD61 | Lead time for T1 | 55 days |
Mold base steel: | P20 | Shot life: | 1 000 000 |
Place of Origin | China | Packaging: | Plywood Box |
High quality,credit comes first,make you much valuable.
JMT Technology has a number of vigorous,forget ahead young people,they keep on chasing the advanced production technology in mould making area,with full passion and the professional CAD/CAE/CAM system operation skill,hass become the backbone of development of JMT Technology.
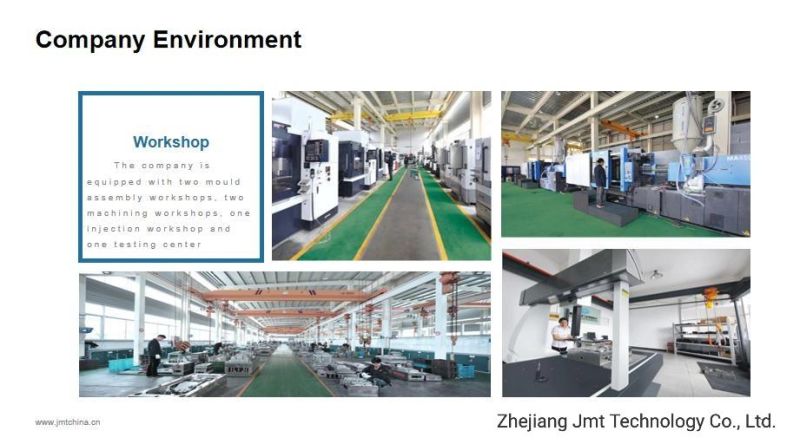
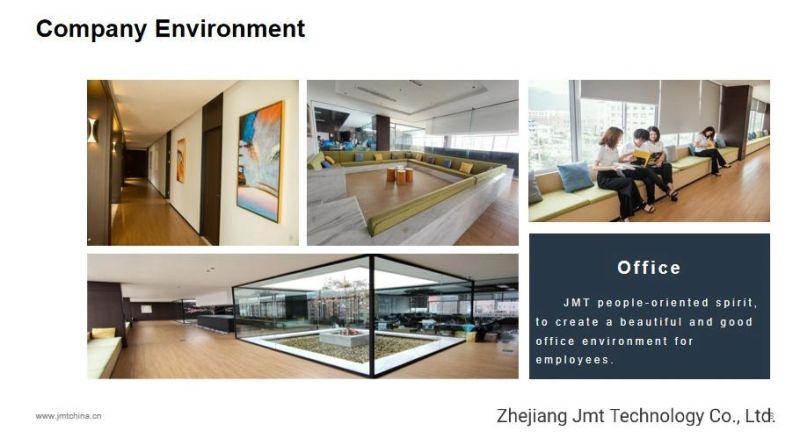
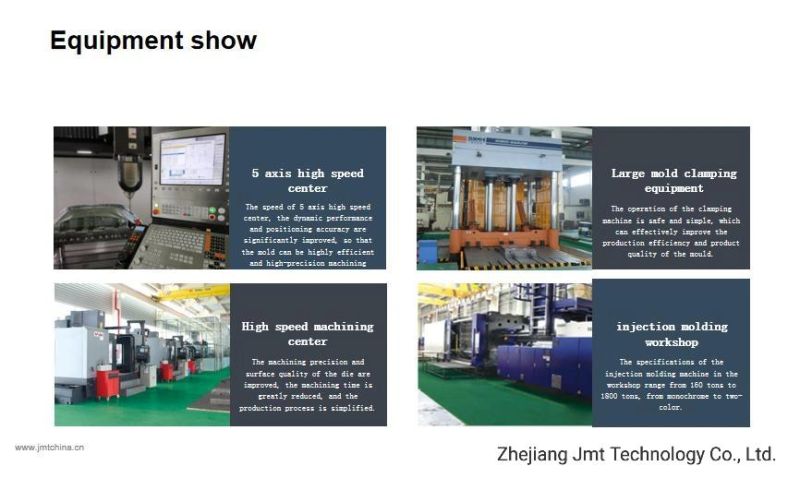
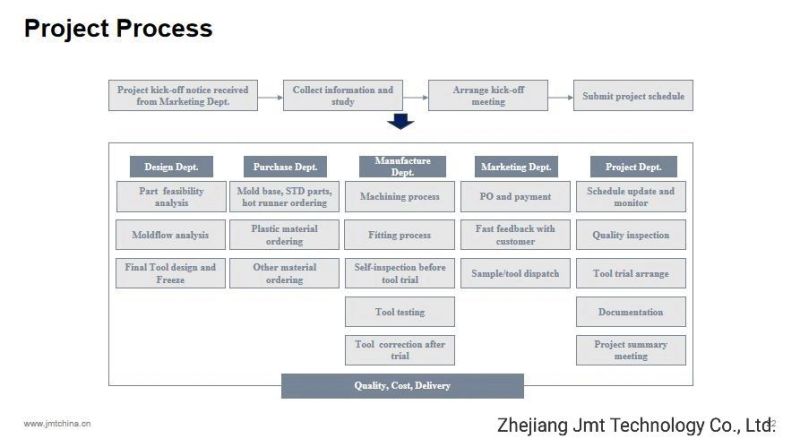
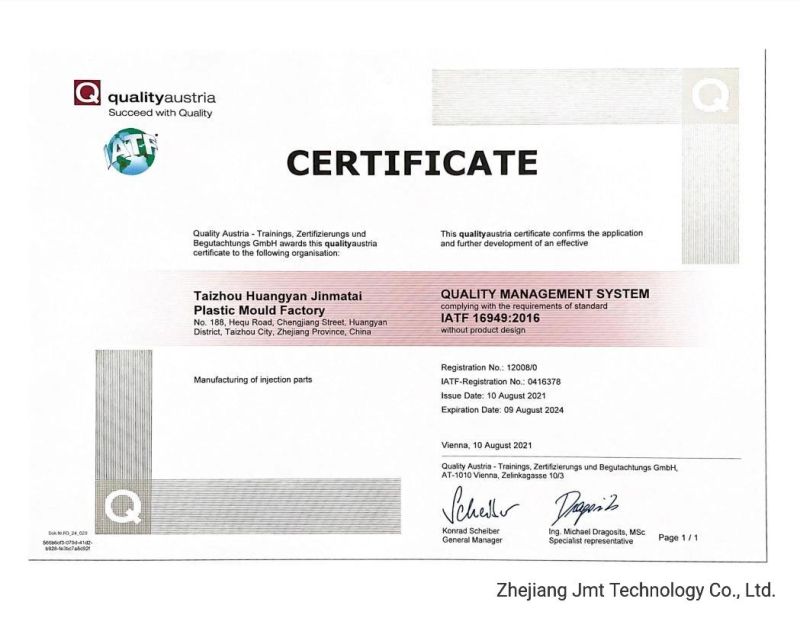
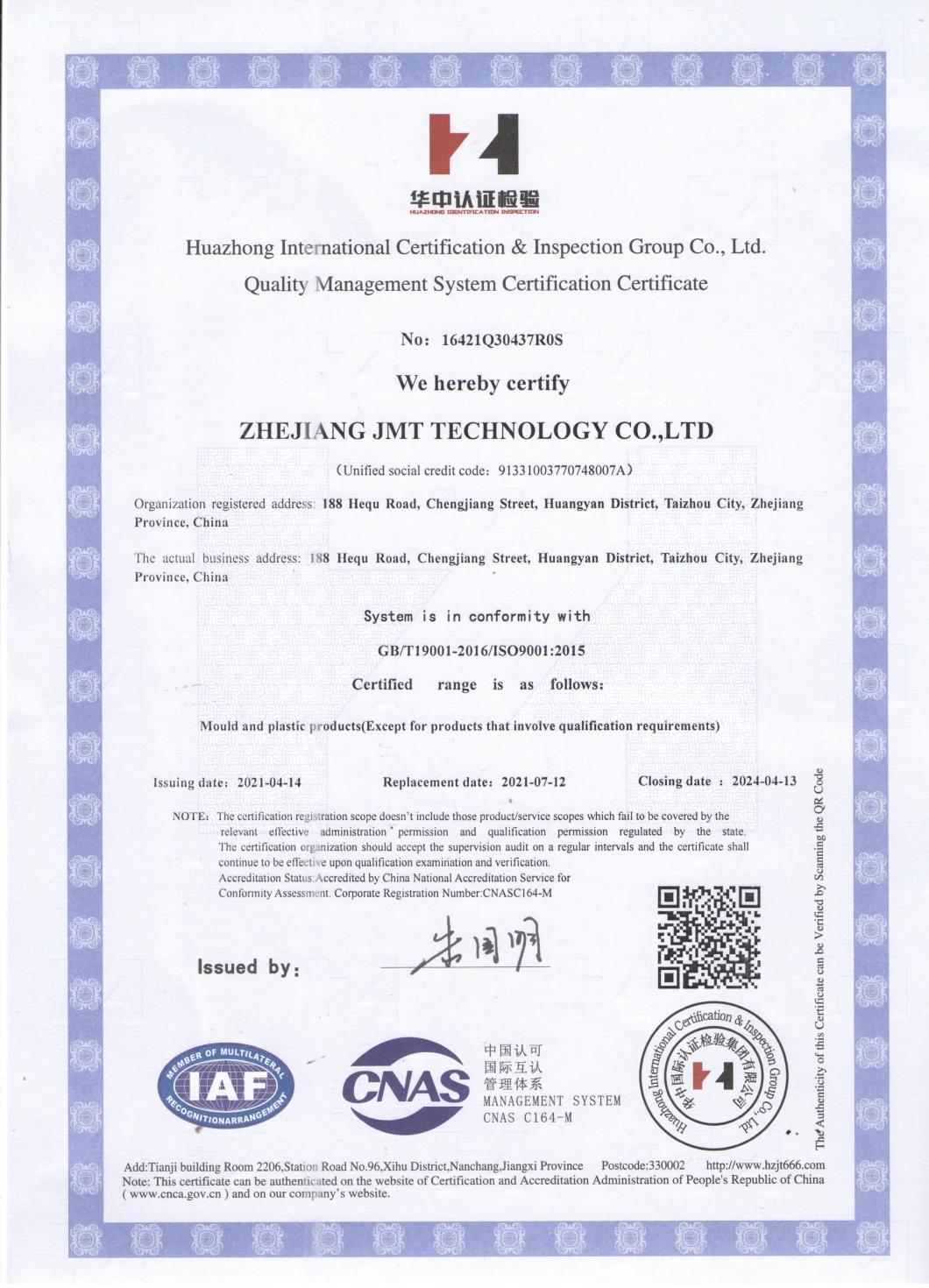
Zhejiang JMT Technology Co.,Ltd specializes in designing and making auto parts, home appliance, kids electric car and household moulds. From 2005 until today, JMT Mould has had many great achievements in plastic mould development and manufacturing. Today, JMT Mould has over two hundred workers, including a mold design team of over 42 engineers.
JMT Mould has organized their facility for efficiency using the latest principles of lean manufacturing. Their capabilities now include prototyping, an injection workshop and a state of the art QC lab. To help realizing the benefits of consistent quality systems and business practices, JMT Mould invested the time and effort to be awarded the ISO/TS 16949: 2009&tISO9001-2015 Quality Certification.
JMT Mould has grown into a superior mold manufacturer with a strong engineering team. Engineering work includes not only mold designs, but also mold feasibility, mold flow, product design expertise and prototyping services. These allow the most efficient mold strategies to be developed for our customers.
We have developed great relationships with customers such as VALEO, MAHLE GROUP, GOODBABY GROUP, by always providing excellent service. We are proud of our culture of continuous improvement and welcome all customers and potential customers to visit our factory anytime.
(1) What is the most important and most decisive factor in choosing mold steel?
Forming method - can be selected from two basic material types.
A) Hot-worked tool steel that withstands relatively high temperatures during die casting, forging and extrusion.
B) Cold working tool steel for blanking and shearing, cold forming, cold extrusion, cold forging and powder press forming.
Plastic - Some plastics produce corrosive by-products such as PVC plastic. Condensation, corrosive gases, acids, cooling/heating, water or storage conditions caused by prolonged shutdowns can also cause corrosion. In these cases, it is recommended to use a stainless steel die steel.
Mold Size - Large size molds often use pre-hardened steel. Integral hardened steel is often used in small size molds.
Mold use times - long-term use (> 1000000 times) of the mold should use high hardness steel, its hardness is 48-65HRC. Medium long-term use (100,000 to 1,000,000 times) today's focus:
The mold should be pre-hardened steel with a hardness of 30-45 HRC. For short-term use (<100000 times), the mold should be made of mild steel with a hardness of 160-250HB.
Surface Roughness - Many plastic mold manufacturers are interested in good surface roughness. When sulfur is added to improve metal cutting performance, the surface quality is thus degraded. Steels with high sulfur content also become more brittle.
(2) What are the primary factors affecting the machinability of materials?
The chemical composition of steel is very important. The higher the alloy composition of steel, the harder it is to process. As the carbon content increases, the metal cutting performance decreases.
The structure of the steel is also very important for metal cutting performance. Different structures include: forged, cast, extruded, rolled and machined. Forgings and castings have very difficult to machine surfaces.
Hardness is an important factor affecting the metal cutting performance. The general rule is that the harder the steel, the harder it is to process. High speed steel (HSS) can be used to process materials up to 330-400HB; high speed steel + titanium nitride (TiN) coatings can process materials up to 45HRC; for materials with hardness 65-70HRC, Carbide, ceramic, cermet and cubic boron nitride (CBN) are used.
Non-metallic inclusions generally have an adverse effect on tool life. For example, Al2O3 (alumina), which is a pure ceramic, has a strong abrasiveness.
The last one is residual stress, which can cause metal cutting performance problems. It is often recommended to perform a stress relief process after roughing.
(3) What are the production costs of mold manufacturing?
Roughly speaking, the distribution of costs is as follows:
Cutting 65%
Workpiece material 20%
Heat treatment 5%
Assembly / adjustment 10%
This also clearly demonstrates the importance of good metal cutting performance and excellent overall cutting solutions for the economic production of molds.
(4) What is the cutting characteristics of cast iron?
In general, it is:
The higher the hardness and strength of cast iron, the lower the metal cutting performance and the lower the life expectancy from the blade and tool. Most types of metal cast iron used in metal cutting production generally perform well. Metal cutting performance is related to structure, and harder pearlitic cast iron is more difficult to process. Flake graphite cast iron and malleable cast iron have excellent cutting properties, while ductile iron is quite bad.
The main types of wear encountered when machining cast iron are: abrasion, bonding and diffusion wear. Abrasive is mainly produced by carbides, sand inclusions and hard cast skin. Bond wear with built-up edge occurs at low cutting temperatures and cutting speeds. The ferrite portion of cast iron is the easiest to weld to the insert, but this can be overcome by increasing the cutting speed and temperature.
On the other hand, diffusion wear is temperature dependent and occurs at high cutting speeds, especially when using high strength cast iron grades. These grades have high resistance to deformation and result in high temperatures. This wear is related to the interaction between the cast iron and the tool, which allows some cast irons to be machined at high speeds using ceramic or cubic boron nitride (CBN) tools for good tool life and surface quality.
Typical tool properties required for machining cast iron are: high heat hardness and chemical stability, but also related to process, workpiece and cutting conditions; the cutting edge is required to have toughness, heat fatigue wear and edge strength. The degree of satisfaction with cutting cast iron depends on how the wear of the cutting edge develops: rapid bluntness means hot cracks and gaps that cause premature cutting of the cutting edge, damage to the workpiece, poor surface quality, excessive waviness, and the like.
Normal flank wear, balance and sharp cutting edges are just what you need to do.